Mitsubishi Materials U.S.A. and Roush Yates Engines Extend Partnership
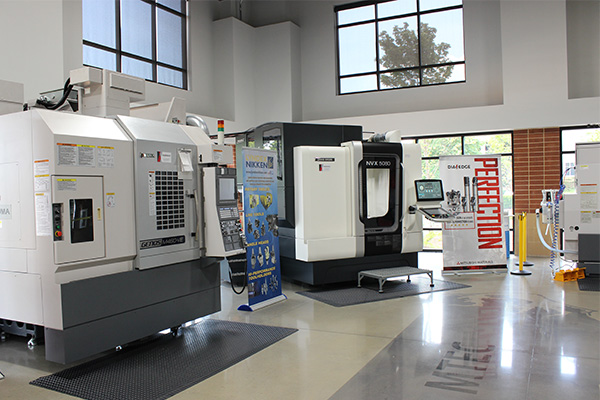
Roush Yates Engines have announced a multi-year partnership extension agreement with Mitsubishi Materials U.S.A. Mitsubishi Materials will continue to be the official CNC tooling supplier of Roush Yates Engines and Roush Yates Manufacturing Solutions.
Mitsubishi Materials U.S.A. has also recently expanded and opened a new 33,000 sq. ft. Machining Technology and Education Center (MTEC) in Mooresville, North Carolina, which provides training to Roush Yates employees.
“Mitsubishi Materials and MTEC is critical to the machining of our high-performance engine components as well as our diversity into other industries,” said Todd English, VP Strategic Partnerships and Marketing of Roush Yates Engines. “We have over 50 state-of-the-art CNC machines at Roush Yates Manufacturing Solutions and we rely on Mitsubishi Materials products and expertise to help us reduce cycle time and tool wear while machining tight tolerances. In addition, their training facility is first class. Our machinists have been able to receive personalized training on new tooling, techniques, and leverage their collective knowledge when working on projects. We look forward to growing our partnership with Mitsubishi Materials and internal growth in order to meet the demands of the marketplace today and as well as innovating for the future.”
Roush Yates relies heavily on Mitsubishi Materials’ cutting tools. They leverage a large array of indexable and solid carbide cutting tools including: tuning, milling, drilling and solid carbide endmills.
“Mike and his team at Mitsubishi Materials play an instrumental role at Roush Yates Manufacturing Solutions,” commented Mitch Miller, VP Manufacturing of Roush Yates Manufacturing Solutions. “As we expanded into our 88,000 sq. ft. CNC facility, we were able to scale up production and flexibility for new projects being included from the aerospace and defense industries. We rely on Mitsubishi Materials to deliver world-class cutting tools to meet our needs and ensure that we are optimizing our machining processes. This is essential for our growth and sustainability in today’s business, where product, precision, quality, and delivery are critical.”