KPI — August 2021: State of Business
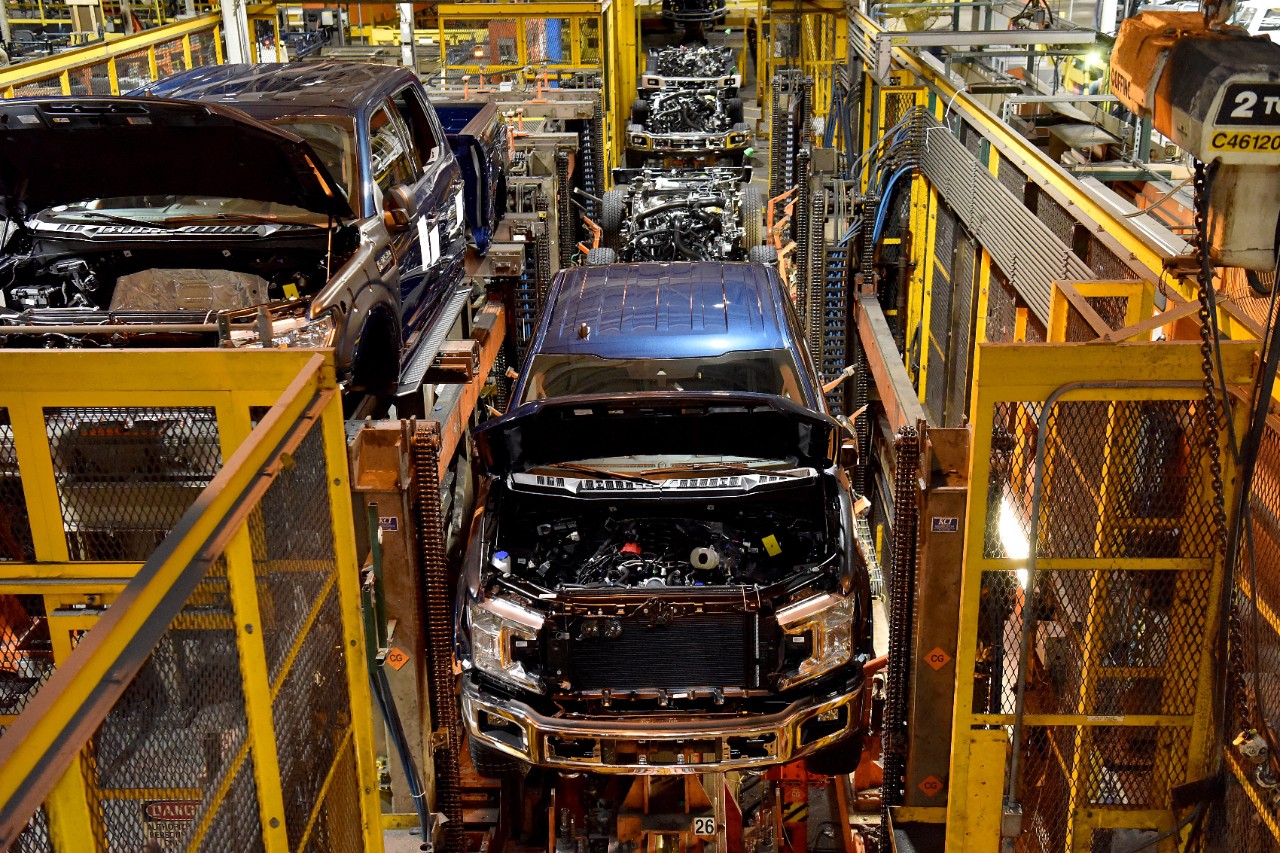
The global chip shortage rages on, with increased demand and constrained capacity choke-holding the automotive industry. During 2020, U.S. semiconductors accounted for half of all global sales, or approximately $193 billion. However, only 12% of those chips are manufactured in the U.S. – a figure that does not include any of the cutting-edge chips required to run more sophisticated technology, according to Fortune.
While the U.S. remains a leader in design, ongoing supply chain challenges, coupled with the development of new semiconductor factories overseas, pose a significant threat – giving China precious leverage, reported Fortune.
“We have fallen very far behind from where we need to be with respect to semiconductors,” said U.S. Commerce Secretary Gina Raimondo. “Semiconductors are the building blocks of our entire digital economy and unfortunately, we’re vulnerable now because we don’t make enough leading-edge semiconductors in America.”
Global Light Vehicle (LV) sales hovered at 82.4 mn units/year in June, marking a slight downturn from an upwardly revised 82.9 mn units/year in May, according to LMC Automotive.
As such, President Biden’s administration is alleged to be planning development of several semiconductor plants in the U.S. as a way to combat the immediate semiconductor shortage and better position the country going forward.
According to reports, Raimondo is preparing to open 6-8 factories within 18 months of Biden signing the Innovation and Competition Act into law – a proposed $250 billion investment in various science and technology fields. It was adopted by the Senate in June and is expected to pass the House.
State of Manufacturing
On the manufacturing side, the July Manufacturing PMI® registered 59.5% – a month-over-month decrease of 1.1 percentage points; though demand, consumption and inputs registered growth compared to June. The data indicates expansion in the overall economy for the 14th month in a row after contraction in April 2020, according to supply executives in the latest Manufacturing ISM® Report On Business®.
“Business Survey Committee panelists reported that their companies and suppliers continue to struggle to meet increasing demand levels. As we enter the third quarter, all segments of the manufacturing economy are impacted by near record-long raw-material lead times, continued shortages of critical basic materials, rising commodities prices and difficulties in transporting products. Worker absenteeism, short-term shutdowns due to parts shortages and difficulties in filling open positions continue to be issues limiting manufacturing-growth potential,” said Timothy R. Fiore, CPSM, C.P.M., chair of the Institute for Supply Management® (ISM®) Manufacturing Business Survey Committee.
High backlog levels, too low customers’ inventories and near record raw-materials lead times continue to be reported. Labor challenges across the entire value chain and transportation inefficiencies are the major obstacles for increasing growth.
Below Kyle Shiminski, vice president and general manager at Warn Industries, Factor 55, Fabtech and Fab Fours, offers his experienced insight on the topic of supply chain.
We are very fortunate to be in an industry – and market segments – where the demand has held up extremely well. In many instances, the demand has grown at rates not many anticipated 18 months ago when we first started seeing the shutdowns as a result of COVID-19. While demand has been incredibly strong, it has clearly put a strain on the supply chain, which extends all the way back to raw materials (steel, aluminum, plastics, cardboard, wood, etc). There likely is not a single base material that is not under immense pressure for demand these days. We continue to work closely with our supply chain to secure materials and components needed to produce our products. We do not see this constraint easing any time soon, so we will continue to provide longer range forecasts to lock in capacity, both with our suppliers and within our own factories.
Like everyone else, in addition to supply chain challenges, we also are seeing logistics constraints. Inbound and outbound freight, both domestically and internationally, is as constrained as we have ever seen it. Inflation costs have grown three and four times in many cases. Unfortunately, we do not see this as something that will just magically ease any time soon and are prepared for the long-haul challenges, while leveraging the combined strengths of our companies to best navigate these issues.
Lastly, labor constraints are as serious an issue as anything else impacting the supply chain. We are actively and aggressively hiring at Warn, Fabtech and Fab Fours; however, we are not seeing the available labor pool like we would have hoped to be seeing by now. We will continue to focus on attracting the best talent available for producing our products and growing our capacity.
We keep saying our current situation is a far better problem to be facing than being in an industry where there is no demand at all but, admittedly, it is extremely frustrating to have to continue to share these challenges with our customers in all of our market segments across the world. Our commitment is – and always will be – to be a consistent communicator and apply 110% effort to meet our customer’s desired needs. Though it is extremely difficult to be in the conditions we are all facing, I am humbled each day by the loyalty of our customers, the passion and dedication of our team members at each of our operations, as well as the commitment to improvement by each of our suppliers all over the world. Fab Fours, Fabtech, Factor 55 and Warn have all weathered storms in the past, and we are poised to weather this one, too – while continuing to deliver more product than ever before. By partnering with our suppliers, logistics and internal resources, we are navigating through this period and coming out of it far better together.
U.S. New Vehicle Sales
Despite manufacturing and semiconductor challenges, new vehicle retail sales continued to set records during July, according to a joint forecast from J.D. Power and LMC Automotive.
Total new-vehicle sales, including retail and non-retail transactions, are projected to reach 1,319,300 units – a 2.7% year-over-year increase but a 12.4% decrease from July 2019, which is attributed to the decline of less-profitable non-retail/fleet sales.
The seasonally adjusted annualized rate (SAAR) for total new-vehicle sales is expected to be 15 million units, up .4 million units year-over-year but down 1.9 million units from 2019.
“Inventory constraints, and its divergent effects on vehicle sales, continues to be the key theme for July. Too few vehicles in inventory mean the sales pace in July is well below the levels seen earlier this year,” said Thomas King, president of the data and analytics division at J.D. Power.
“Conversely, the lack of inventory is driving the price of the vehicles to record highs as manufacturers and retailers continue to dial back discounts. While the quantity of sales is down, the quality of each sale is up, evidenced by the fact that consumers will spend more money buying new vehicles than ever before in the month of July, and dealer profits from selling new vehicles will reach an all-time high,” he added.
Important Takeaways, Courtesy of J.D. Power:
- Dealers currently have 932,000 vehicles available for retail sale, compared with 3.1 million two years ago. While new inventory is arriving at dealers daily, it is being sold almost as quickly as it arrives.
- Consumers are on pace to spend $48.7 billion on new vehicles – a record for July, a $9.9 billion year-over-year increase and $8.8 billion rise from July 2019.
- The average new-vehicle retail transaction price in July is expected to reach a record $41,044. The previous high for any month was $39,942, set in June 2021.
- Total retailer profit per unit, inclusive of grosses and finance & insurance income, are on pace to reach an all-time high of $4,260 – a year-over-year increase of $2,230 and the first time above $4,000.
- Trucks/SUVs are on pace to account for 76.5% of new-vehicle retail sales in July.
“Looking forward to August, the dynamics observed in July are expected to continue. Inventory levels will not improve meaningfully in August and the sales pace will be depressed as many shoppers fail to find their desired vehicle,” explained King. “However, buyers who do find their desired vehicle will pay higher prices. The silver lining in this environment is that manufacturers and retailers will realize extraordinary profits on every unit that is sold, and in many cases the per-unit profit will more than offset the drop in volume.”
U.S. Used Market
Wholesale used vehicle prices (on a mix-, mileage- and seasonally adjusted basis) decreased 2.6% month-over-month in July. This brought the Manheim Used Vehicle Value Index to 195.2, a 23.6% increase from a year ago.
According to the most current report, the Manheim Market Report (MMR) prices posted weekly declines every week in July, with price declines accelerating through mid-month but then slowing the rate of decline over the last two weeks. Over the last five weeks, the Three-Year-Old Index declined a net 3.6%.
All major market segments posted year-over-year, seasonally adjusted price increases during July. Vans, pickups and sport utility vehicles had the largest year-over-year performance, while the remaining car segments lagged the overall market, noted Manheim.
Overall, total used vehicle sales were down 15% year-over-year in July. Manheim estimates the used SAAR to be 38.5 million, down from 44.8 million last July and 39 million recorded in 2019. The July used retail SAAR estimate is 21.5 million, down from 23.7 million last year and up month-over-month from June’s 21.3 million retail SAAR.
KPI August 2021: Recent Vehicle Recalls
Key Performance Indicators Report — August 2021