A Four-Cylinder Turbo Engine Unlike Any Other
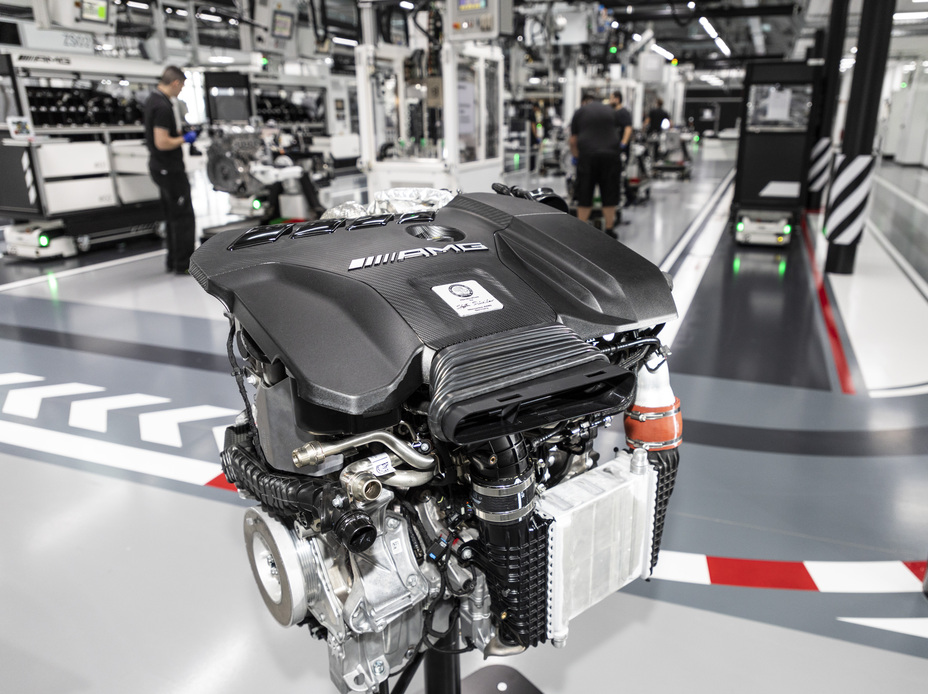
The completely newly developed Mercedes-AMG 2.0-liter M 139 engine is the world’s most powerful turbocharged four-cylinder engine in series production, according to Mercedes-AMG. With an output of up to 416 horsepower, the new engine exceeds the company’s previous M 133 engine by 40 horsepower. Maximum torque has also increased from 350 lb-ft to up to 369 lb-ft.
The new, highly efficient engine is produced on an innovative production line in Affalterbach, Germany.
The four-cylinder engine is available in two output versions for the compact models of Mercedes-AMG: with 416 horsepower for the S-model and 382 hp in the base version. This product policy logic has already proved successful in the V8- powered AMG Performance models, and more closely meets customer wishes.
Apart from its performance figures, the new engine impresses with its immediate response, according to Mercedes-AMG. To this end, the torque curve was balanced with torque shaping: The peak torque of 369 lb-ft (354 lb-ft for the base version) is available in a range of 5,000-5,250 rpm (4,750-5,000 rpm in the base version).
With this configuration, the AMG engineers have achieved a power delivery similar to that of a naturally aspirated engine for an even more emotional driving experience, according to the company. The engine developers were also able to realize a dynamically increasing torque curve in the lower engine speed range, thereby improving agility.
180-Degree Rotation
Compared to the transversely installed M 260 four-cylinder in the 35 models or the preceding M 133 engine, the new Mercedes-AMG M 139 is rotated around its vertical axis by 180 degrees. This means that the turbocharger and the exhaust manifold are positioned at the rear, on the side of the firewall when viewed from behind. The intake system is therefore positioned at the front. This configuration allows the flattest possible and aerodynamically advantageous front section design, according to Mercedes-AMG. Furthermore, the new arrangement allows for improved air ducts with shorter distances and fewer diversions – both on the intake and exhaust side.
Roller Bearings
The new twinscroll turbocharger combines optimum responsiveness at low engine speeds with a high power in the upper rpm range. In addition to this, the turbine housing is divided into two flow passages that run parallel to one another. Together with the divided ducts in the exhaust manifold, this makes it possible to feed the exhaust flow to the turbine separately.
The aim is to prevent the individual cylinders from influencing each other negatively during load cycles, and to improve the gas cycle. The result is higher torque at lower engine speeds, and extremely quick responsiveness.
Furthermore, the shafts of the compressor and turbine have roller bearings for the first time-”similar to the top output variant of the AMG 4.0-liter V-8 engine in the AMG GT four-door Coupe. The roller bearings reduce mechanical friction within the turbocharger to a minimum. The charger therefore responds more readily and reaches its maximum speed of up to 169,000 rpm more rapidly.
Electronic Charge Pressure Control
With a maximum charge pressure of 2.1 bar (1.9 bar in the base version), the 2.0-liter turbo engine is also a top performer in this respect. The electronically controlled wastegate (exhaust relief valve) allows the charge pressure to be controlled even more precisely and flexibly while optimizing responsiveness, especially when accelerating from partial load. Numerous parameters are taken into account in this process.
The main input signals for the wastegate control unit are the charge pressure, throttle flap position and the knocking tendency. The modifying signals include the intake air temperature, engine temperature, engine speed and atmospheric pressure. This also makes temporary boosting of the charge pressure (overboost) possible under acceleration.
Fresh air is used in addition to oil and water to cool the turbocharger. This is directed specifically to the charger from the radiator grille, via the engine cover designed as an air deflector and ducts beneath the hood.
The concept is based on the principles and experience gained with the cooling for the internally mounted turbochargers of the current AMG 4.0-liter V-8 engines, starting with the AMG GT in 2014. In addition, the turbine housing incorporates integral insulation.
Crankcase Advantages
The all-aluminum crankcase is a chill-cast unit, which excels with outstanding material properties. In this process, the molten aluminum is poured into the metallic mold. Thanks to its good thermal conductivity, the water-cooled mold allows rapid cooling and solidification of the melt, according to Mercedes-AMG. The result is a fine-grained, dense structure that guarantees very high strength. Complex interior geometries can be realized with the help of enclosed sand cores.
The closed-deck construction-”a design from motor racing-”ensures outstanding rigidity with low weight and allows peak combustion pressures of up to 160 bar, according to the company. The areas around the cylinders are mostly solid; only smaller ducts for the coolant and engine oil penetrate the cover plate.
The crank assembly with a lightweight, forged steel crankshaft and forged aluminum pistons with optimized piston rings combines low friction with high strength. The sump features baffle plates so that despite the larger sump, and even under high lateral acceleration forces, there is always sufficient engine oil to lubricate all the relevant components.
NANOSLIDE Coating
To reduce friction between the pistons and cylinders, the linings are coated using patented NANOSLIDE technology. This gives the linings a mirror-like surface for minimal friction, is twice as hard as conventional grey cast-iron liners and therefore makes them much more durable. NANOSLIDE was developed by Daimler AG. The coating was first used for AMG’s M 156 engine, has benefitted further AMG engines for many years and can also be found in the Formula 1 engine of Mercedes-AMG Petronas Motorsport.
Larger Exhaust Valves
Repositioning and slightly angling the injection nozzles and spark plug system in the cylinder head made it possible to enlarge the exhaust valves compared to those of the preceding M 133 engine, according to Mercedes-AMG. The larger exhaust cross-sections allow the gases to stream out of the combustion chambers with low losses, and reduce the overall piston venting action.
More efficient cylinder head cooling was achieved by seating rings with a reduced installed height and a cooling borehole near the combustion chamber, in the web area between the exhaust seating rings. The cooling performance was also improved by a near-surface water jacket geometry, a faster flow rate and an optimized volumetric flow rate.
A multi-layered, state-of-the-art corrugated metal seal isolates the cylinder head from the crankcase.
Two overhead camshafts control the 16 valves via weight-optimized roller cam followers. Camshaft adjustment on the inlet and outlet side allows an excellent response and optimizes the gas cycle for each operating point. Variable CAMTRONIC valve control on the exhaust side is another feature, with two cams per valve.
The cams have different geometries, so that depending on the cam setting to suit the driving situation, the exhaust valves can be opened for short or long periods -“ for even better responsiveness at low engine speeds, comfortable and fuel-efficient driving at medium rpm and full power delivery in the upper rpm range.
Turbocharging, Fuel Injection
Turbocharging and direct injection with a spray guided combustion process not only allows for a high-power yield, but also improves thermodynamic efficiency and therefore reduces both fuel consumption and exhaust emissions, according to Mercedes-AMG.
For the first time, the new high-performance four-cylinder has two-stage fuel injection. In the first stage, the particularly fast and precisely operating piezo injectors supply fuel to the combustion chambers at a pressure of up to 200 bar. This is a multiple process at times and is controlled by the engine management system as required.
In the second stage there is additional intake manifold injection using solenoid valves. This is needed to achieve the engine’s high specific output. The electronically controlled fuel supply has an operating pressure of 6.7 bar.
Cooling System
The high output requires an intelligently conceived cooling system. An additional radiator in the wheel arch supplements the large unit in the front level of the main module. A low-temperature circuit is also used for air/water intercooling. Together with the intercooler connected in series, a high-performance electric pump assists the coolant flow through the radiators. This provides for ideal cooling of the highly compressed charge air, thereby contributing towards optimal engine performance, according to Mercedes-AMG.
Cooling of the transmission oil is integrated into the engine’s coolant circuit and is assisted by a heat exchanger mounted directly on the transmission. The engine control unit is mounted on the air filter housing, where it is cooled by an airflow.