3D Printing & Scanning Help Keep Hot Rodding Alive
The birth of in-shop design systems have helped make building customs more accessible...
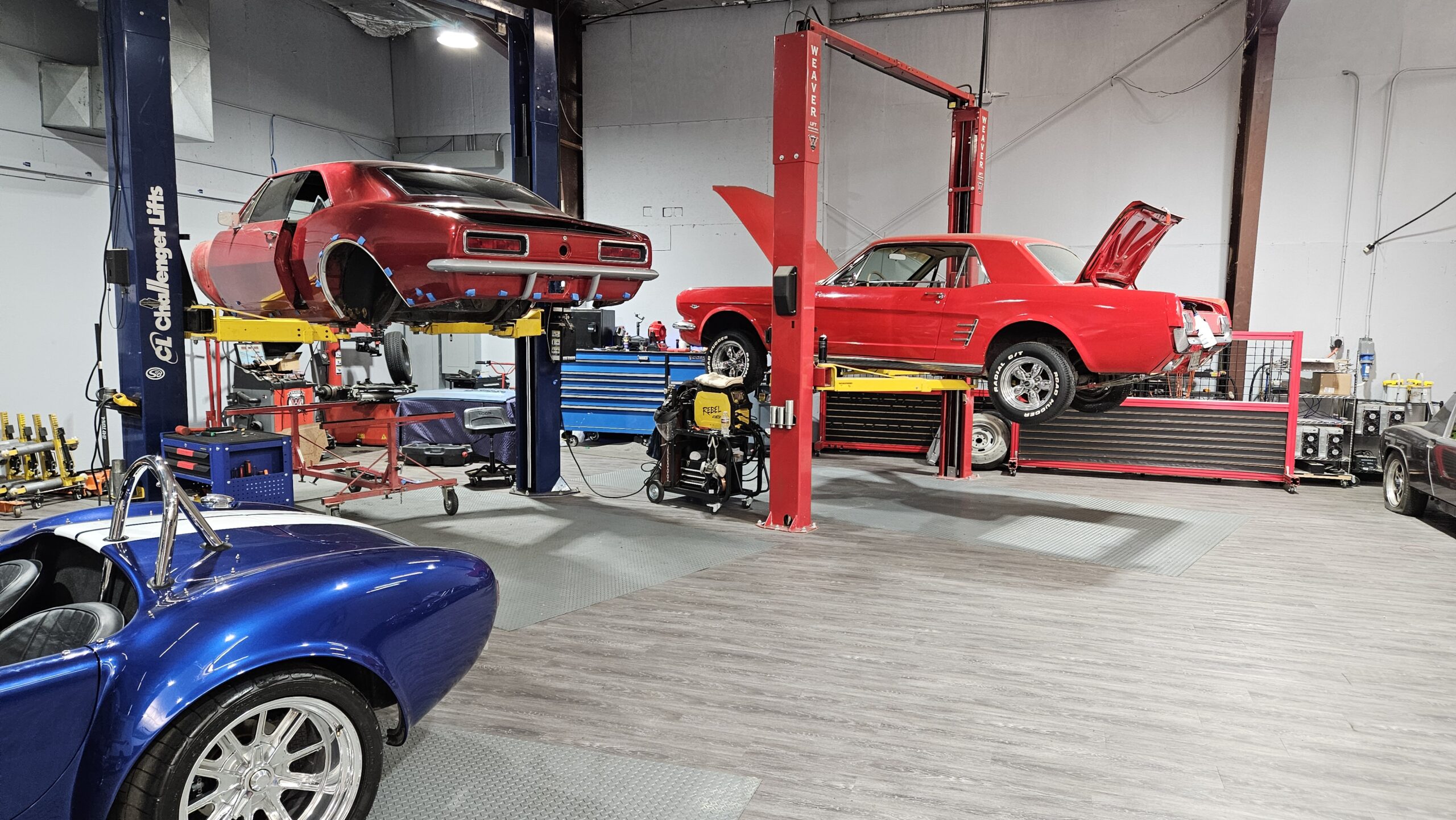
As aftermarket part offerings are constantly growing and changing, a new article from Motortrend highlights some of the ways that modern technology has helped bridge the gap when it comes to custom and one-off parts.
For many years, hot rodding took countless hours of welding and metalwork but now, thanks to technologies like Computer Assisted Design (CAD), Computer Numerical Control (CNC), Solidworks and 3D printing, many shops have jumped into the modern tech era. Shops like Detroit Speed use a variety of computers and Solidworks virtual imagery software to design and develop many of their builds on the computer before they come to life, according to the article.
While there’s still plenty of room for master welders, metal shapers and painters, many of these recent technologies have helped make the build process much faster, and helped to keep low-production parts available for even the at-home DIYer.
At the same time, many of these systems are quite expensive but can be hugely beneficial for a shop building customs that require unique drivetrain packaging, and help to overcome the age-old issue of designing a build with ease of manufacturing in mind.
One major development that has helped numerous builders around the country is the development of 3D scanning, where highly-detailed scanners can transfer data around a car down to thousandths of an inch. Coupling 3D scanning with 3D printing can help design full interiors, low-clearance powertrains and help ease the burden of building precise fitting parts before billet parts would be machined, saving builders both time and money.
To read the full report from Motortrend, click here.